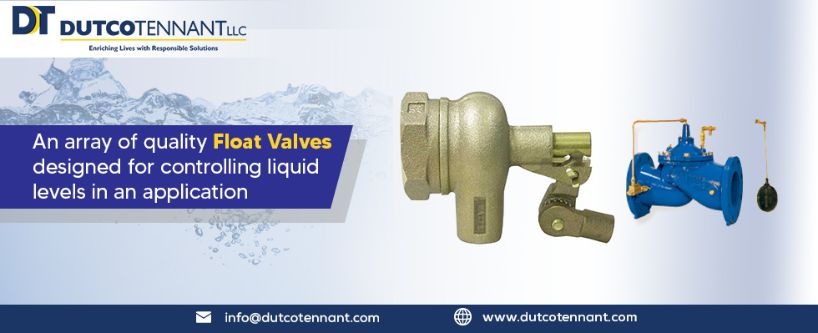
A Quick Guide to Select Float Valves
The control over liquid levels is one of the key considerations when it comes to safety and overall function of facilities in the processing industries that includes gas and oil, food, chemical industries as well. The installation of a float valve is commonly done to regulate the liquid level or flow within a tank.
Float valves are also referred to as ball-cock valves. Since the use of float valves is employed in a varied range of applications and industries, the float valves are absolutely mechanical in their operations.
But when it comes to the selection of float valves, consumers can deal with overwhelming feelings because of the array of brands and types available in the market. In this guide, we help out to pick the most suitable float valves for your application by enumerating the key things that you need to know about this device.
Keep reading till the end to learn all about float valves.
The Primary Purpose of a Float Valve
The main purpose of the float valve is to regulate the fluid flow, fill the level of the tanks and cease overfilling or overflow while the valve connector attaches the valve to the incoming liquid. When the float rises and reaches to the determined level, the valve is then opened or shut down by the lever connected to the float.
All the components comprising the valve, connector and float work simultaneously to ensure that the liquid remains at the perfectly set level with the requirement for minimal monitoring by the technicians.
Types of Float Valves Available
There are mainly two types of available and they are -
- Direct Float Control Valve
- Pilot Operated Float Control Valve
Direct Float Control Valve
In this type of float valve, the float rises with the rise of liquid level in the tank. Here, the main valve opens or shuts by the movement of the float valve arm unit.
Designed with an assembly of controller, measurement device and a final control device all built in a single unit. The measurement is itself the ball-float.
Pilot Operated Float Control Valve
In this type of valve, when the liquid level in the tank increases, the float raises to shut the pilot valve. The developed liquid on the upper chamber of the primary control valve.
The upper chamber includes a diaphragm that exerts pressure over the primary valve to shut. The float settles down as with the liquid level and enables for liquid to pass through the float valve’s pilot line. Now, the main valve functions to open that allows the liquid to fill in the tank.
Selecting a Float Valve
The selection of a float valve must be done depending upon the following process limitations -
- Operating temperature differs with PVC or metal float, float material must be considered carefully while choosing.
- Maximum pressure.
- Typically for water level applications, non-corrosive material should be taken into consideration.
So, what are you waiting for? Now that you have a basic guide to refer to, make sure to choose the ideal float valve for your application now.